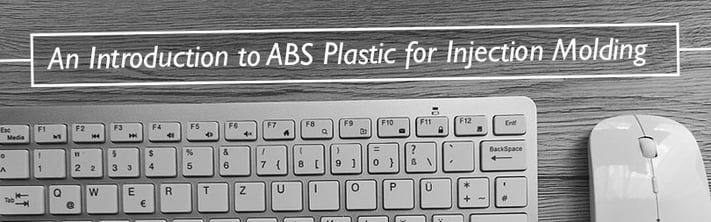
ABS is an acronym for acrylonitrile butadiene styrene. (Now you understand why it goes by its initials!) It is an opaque thermoplastic polymer. The term “thermoplastic” refers to a class of plastics that can be reprocessed after an initial heat cycle; as opposed to "thermoset" plastics that undergo an irreversible chemical change during its first heat cycle. ABS is a common engineering grade plastic and it is used in many products around you, particularly electronic enclosures.
Physical Characteristics of ABS
The nitrile groups in ABS make it stronger than pure polystyrene, and its styrene component gives it a shiny, protective surface. The polybutadiene in ABS is rubbery in consistency, which provides impact strength and durability.
ABS is resistant to many chemicals and electrical current. ABS is lightweight and easily machined, sanded, painted, and glued. It can also be colored and textured relatively easily. Specialty grades can include flame retardants to meet a regulatory requirement or fiberglass fillers to improve stiffness, acting like rebar in concrete.
Its low melting temperature not only makes it ideal for injection molding, but for other applications such as 3D printing. Thus, the transition from a 3D printed prototype to production can be fairly smooth. It is a relatively inexpensive material, with a cost that typically falls between that of polypropylene and polycarbonate. These characteristics help explain why it is widely used across many product types and industries, and is an excellent choice for prototyping.
Prolonged exposure to sunlight's UV rays will weaken or embrittle ABS, so it isn't a great fit for outside applications. With a low softening point, ABS is not used in applications that require high heat resistance. However, additives mixed with the resin pellets can increase its heat resistance to an operating range of as high as 176 degrees Fahrenheit. Lastly, there are certain substances that will also weaken ABS, so it is important to consider what substances your product might face in the real world and check with your molder or material manufacturer.
What Types of Products are Made with ABS?
If a product must be light, shock absorbent, and possibly chemical resistant, there’s a good chance it will made of ABS. Some of the more common uses include:
- Automotive trim components
- Protective carrying cases and luggage
- Enclosures for many electronics
- Protective headgear
- Musical instruments like recorders and plastic clarinets
- Small kitchen appliances
- Computer keyboards and keycaps
- Plastic toys, including common building blocks
Is ABS Right for Your Next Project?
If you are considering using ABS for your next plastic injection molding project, we’re happy to answer any questions you have about it. We use it often and are very familiar with its properties. Give us a call, or tell us about your project!
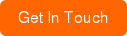