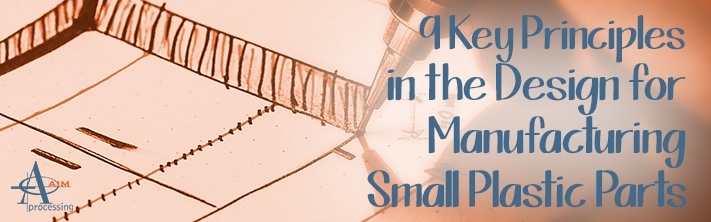
Design for manufacturing (DFM) is an approach to product development that emphasizes the importance of designing a product in such a way that it is easy to manufacture. Also known as design for manufacturability, it is used in a wide range of engineering disciplines, including the injection molding of small plastic parts. Through the smart application of DFM principles to everything from the raw materials used to dimensional tolerances to the number of components in a finished part, companies can often produce more parts faster and at a lower cost.
Designing for Plastic Injection Molding: Keep it Simple
As you begin work on developing your next product or enhancements to an existing one, here are nine DFM principles you should follow:
- Minimize the number of components. The more seams or connections a finished part has, the more places it has to fail. Simple parts with fewer elements are more reliable, easier to assemble, and they are also subject to fewer inventory control issues.
- Use standard components when possible. If you can utilize commercially available and field-tested components rather than custom designing each piece, you eliminate a number of potential problems.
- Use parts that you’ve designed across product lines. Rather than “recreating the wheel” many times over for your many different products, engineer new products to use as many common parts as possible.
- Design with fabrication in mind. This includes using shapes that are easy to mold, avoiding the need for surface finishes that require additional work, etc.
- Limit the number of machine operations required. The higher the number of “ops” required, the longer it will take to create a small plastic part, and the more opportunities for error are introduced.
- Design with tolerances that are not difficult to achieve. Rather than pushing the systems used to create a part to their limits, capitalize on smart design to achieve outstanding finished products.
- Take assembly processes into account in your design. The easier it is to assemble a part, the faster they will be assembled and the fewer problems will arise. Be sure there is no ambiguity in the way things go together.
- Minimize the need for adjustments. While the ability to “fine-tune” a part may seem like an advantage as you design it, when you get to the manufacturing stage, it becomes more work and leaves you at risk of delivering parts that are out of adjustment.
- Consider how a design impacts the packaging and shipping of parts. Items that can prepared for delivery quickly and with less packaging simplify the tail end of the manufacturing process and ultimately save you money.
We Know Good Design When We See It
Our experienced team has been in this business long enough that we can tell from a quick glance at a drawing or even a verbal description just how easy or difficult it will be to manufacture a small plastic part. If you’ve got questions about how the DFM principles apply to your next project, don’t hesitate to get in touch with us by stopping by our facility in the Denver area or clicking the link below. We’re happy to talk about what you’re trying to accomplish and the best way to do it.
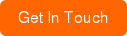