Insert molding is a technique in which an item such as a threaded fastener, tube or stud, electrical component, or label is present in the mold. As the viscous plastic fills in around it and hardens, the item becomes a component of the finished part. When performing insert molding, it’s obviously critical that the insert does not move as the mold closes or as plastic is injected under pressure into the cavity — no small feat as hot resin can enter at 20k-30k psi.
Horizontal vs Vertical Tooling
Holding parts/components in place when the mold closes is key to successful insert molding. Your part design will affect your choice of horizontal or vertical tooling and the challenge of holding your part in place. Horizontal injection molding tooling is more common today and is more interchangeable between machines. The mold opens and closes on a horizontal path, with gravity assisting in the ejection of the parts.
Vertical injection molding tooling is less common and not as interchangeable. Vertical machines open/close on a vertical plane, but the plastic can be injected from either a horizontal or vertical plane, depending on the equipment capabilities. The advantage of vertical tooling is that you can let gravity handle the issue of holding the part during mold closing. It’s also easier for the machine operator to access the completed parts. And since the parts don’t fall to the floor, they can be handled with more care.
Preload, Part Dimensions, and Shutoffs
In order to hold parts/components in place during the injection phase, there should be an interference or preload on the inserts of about 0.005” – 0.008”. This helps ensure that the pressure of the incoming resin doesn’t dislodge the components, sending plastic into spaces where it shouldn't be.
Using insert components with reliable dimensions is important. Part-to-part and batch-to-batch variability must be controlled. Another crucial element is establishing the right kinds of shutoffs. Doing so will improve the longevity of tooling and reduce cosmetic flash that can result from weak shutoffs.
Quick Tips for Insert Molding
With the above factors in mind, here are some tips for ensuring that your components stay in place, resulting in high quality finished parts:
- Have a plan for holding the parts/components steady during mold closing
- Select & source inserts that have reliable dimensions
- Establish the right preload to hold the part during the plastic fill phase
- Consider shutoff surfaces and reveals that will control flash and improve tool-life
Trust Our Insights on Inserts
If your next project calls for insert molding, you’ve come to the right place. We’ve got a nationwide reputation for our expertise in this area, and we’re happy to share our insights. Give us a call.
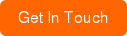