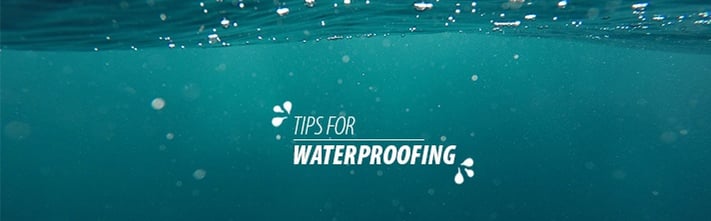
If an enclosure you are developing has to be waterproof, there are a number of issues you must consider. The first, somewhat surprisingly, is terminology. The word “waterproof” can be a bit of a catchall, meaning “watertight,” “water resistant,” “water repellant,” etc. depending on who you are talking to.
When talking about waterproofing, it’s important to ensure that everyone involved is speaking the same language. That vocabulary should use what are called “Ingress Protection Marking” numbers or “IP ratings.” These ratings define how effective the sealing of an enclosure must be to solids (e.g., dust) and liquids (commonly water). When developing a product to meet the needs of your customer, knowing the standard is the place to start.
Keep it Simple When Sealing
The key to effective waterproofing is keeping the design of the end product as simple as possible. Basic shapes, basic interfaces, minimal parting line changes, etc. Here are six tips on how to achieve the highest IP ratings.
- Take advantage of circles. Circles are the ideal shape for openings in a waterproof electronic enclosure, in part because of the availability of a wide range of o-rings and radial-type seals. These items can exert continuous, uniform force around a circumference.
- Avoid complex seals. If possible, design your parts to minimize the need for seals between three or more parts. The more complex the interface, the harder it is to achieve adequate and uniform gasket compression.
- Ensure proper support when using gaskets. Stand-alone gaskets must have as much support as possible on all sides. Leaking or full seal failure can occur from a gasket pulling out of the pinch zone, particularly if there is internal or external pressure involved.
- Consider what will distort and shrink. Stiffer parts are easier to seal because they will fight the resistance to open. Corners, zones of distortion, are a common culprit in turning your intentions of an immersible device into a water resistance device. Very difficult to overcome later.
- Compressive forces are more reliable. Wedge-fit components make it difficult to control sealing forces. Look for a way to apply a uniformly distributed compressive force on your sealing surface. A common technique is a bulkhead fitting.
- Tortuous path. Even if they don't wear them both, many engineers like to think in terms of "belts & suspenders". A single sealing surface can be effective, but designing a stepped path of sidewalls and sealing surfaces is often easier to design on the front end and will give you an added measure of safety.
Options Beyond O-Rings and Gaskets
Because of their cost effectiveness, o-rings and gaskets are commonly used for sealing enclosures. However, there are other methods that produce great results. They include:
- Elastomeric overmolding: In essence, your sealing material is bonded directly to one half of your enclosure. Pros: ability to seal complex edges or shapes without worrying about gasket placement. Cons: more tooling.
- Ultrasonic welding: Through ultrasonic agitation, your two pieces melt and fuse together. Pros: this can be impenetrable in many applications. Cons: cannot take it apart and may require special fixturing.
- Liquid adhesive or RTV: Dosing a small amount of adhesive or RTV into interfacing surfaces. Pros: very inexpensive. Cons: may not be able to take apart and may not be compatible with all plastics.
Keep these options in mind when you are beginning your project.
When You Need to Keep Water Out
Waterproofing an electronic enclosure can be a significant challenge, but it’s one we’ve been helping customers meet for more than 20 years. If you need to keep water out, give us a call and we’ll share our thoughts on how to approach your project.
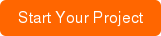